Batch Manufacturing Records
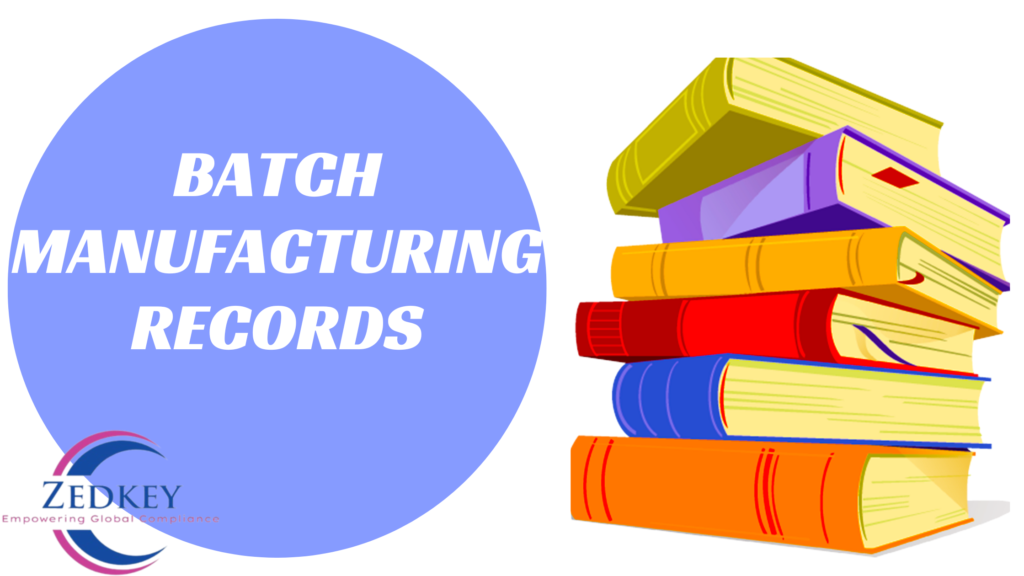
Introduction to Batch Manufacturing Records (BMR)
Batch Manufacturing Records (BMR) are the backbone of pharmaceutical manufacturing. These documents capture every detail of the production process, ensuring consistency, traceability, and compliance with regulatory standards. Without a proper BMR, the safety and quality of a product cannot be guaranteed, making it a critical component in producing life-saving medicines.
Definition of a BMR
A Batch Manufacturing Record is a comprehensive document that records all details of a specific batch of a product. It includes information about raw materials, equipment, production steps, quality checks, and final outcomes. Essentially, a BMR acts as both a guide and a record, ensuring that each batch meets predefined standards.
Purpose of a BMR in Pharmaceutical Manufacturing
The primary purpose of a BMR is to ensure that every batch is manufactured consistently and adheres to regulatory guidelines. It serves as evidence that the manufacturing process followed Good Manufacturing Practices (GMP), helping companies meet global quality and safety standards. BMRs are crucial for audits, recalls, and troubleshooting any issues in production.
Key Components of a BMR
A well-maintained BMR includes the following essential sections:
- General Information: Batch number, product name, and date of production.
- Raw Materials and Components: Details about raw materials, including lot numbers and quantities.
- Equipment Details: Information about the equipment and its calibration status.
- Manufacturing Process Description: Step-by-step documentation of the process, including mixing, granulation, and blending.
- In-Process Quality Control (IPQC) Tests: Data from intermediate tests to ensure process consistency.
- Packaging and Labeling Information: Instructions and records for the packaging process.
- Storage and Handling Instructions: Guidelines for storing and handling the finished product.
- Final Batch Release Signatures: Approval from authorized personnel to release the batch.
Steps Involved in Preparing a BMR
Creating a BMR involves:
- Referencing the Master Formula Record (MFR).
- Documenting raw material usage and equipment setup.
- Recording each step of the manufacturing process in real-time.
- Capturing in-process and final quality control test results.
- Reviewing and approving the BMR before the batch is released.
Role of BMR in Regulatory Compliance
BMRs are critical for meeting the stringent requirements of regulatory agencies like the FDA, EMA, and WHO. They provide documented proof that a product was manufactured according to GMP guidelines, making them essential during audits, inspections, and product registrations.
Significance of BMR in Ensuring Product Quality and Safety
BMRs ensure that every batch meets the required quality standards by documenting:
- Correct raw materials and quantities used.
- Adherence to process parameters.
- Proper functioning of equipment.
- Successful completion of quality control tests.
Without a BMR, it would be impossible to verify that a product is safe for use.
Common Mistakes to Avoid When Preparing a BMR
Mistakes in BMR preparation can lead to costly delays or compliance issues. Common pitfalls include:
- Incomplete Data: Missing information on raw materials or test results.
- Inconsistent Documentation: Using non-standard formats or failing to record deviations.
- Illegible Handwriting: For paper-based BMRs, this can lead to errors.
- Failure to Follow MFR Instructions: Deviating from the approved process without proper documentation.
- Lack of Signatures or Approvals: Missing approvals can invalidate the entire record.
Avoiding these errors ensures smooth audits and high-quality production.